Gary Caunt joins Power Jacks as Manufacturing and Continuous Improvement Director
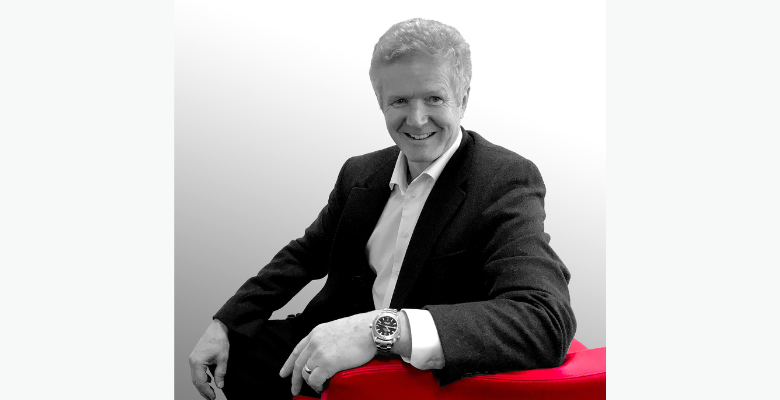
Power Jacks is delighted to share the appointment of Gary Caunt into its new role of Manufacturing and Continuous Improvement Director. Gary joined the business on the 31st of October 2022 and will be responsible for overseeing the manufacture of all our products on the shop floor whilst introducing Lean methodologies including SMED (Single-Minute Exchange of Die), to build on the strong 5S foundation already in place.
Gary shared of his appointment,
“I have been familiar with Power Jacks for several years and have also worked with the business previously on a consultancy basis. What’s fantastic to see is the vast knowledge and skills we have within the company, and I am focused on drawing out the talent of our team whilst driving performance improvements on our shop floor.”
Gary started out as an apprentice to trade in iron and steel and what follows is an impressive manufacturing career including roles at Baxters Food Group, Hydro Group and GE Lighting where he has his name on two patents relating to high intensity metal halide lamps. Gary is also a qualified member of the Institute of Directors having held two previous director roles, as well as a non-executive position, all in engineering.
Having been involved with Power Jacks previously, Gary is familiar with our team and has been impressed with their willingness to take on new ways of working. He shares,
“When working with Power Jacks as a consultant I was involved in training many of the workshop and management team, introducing the 5S method with the goal of driving down waste and reducing the number of errors made. This was 3-years ago now and I have been pleased to see that the team have stuck at it and really bought into it.”
Gary is focused on streamlining our manufacturing processes with the priority of increasing capacity to support our growth potential. As part of this, Gary has spent time in his first few weeks getting to know the team and better understanding everyone’s strengths and weaknesses. He shares,
“It was important for me to get to know the team on a personal level from the outset, so I have had 1-2-1s with each individual. This allowed me to gauge how everyone works and where we need to improve.
“I’ve also been enjoying getting to know the product range as this is new for me and as an advocate for continuous improvement, it’s been interesting to learn how our products can improve efficiency, enhance accuracy and lower costs across so many applications.”